1MW 2MWh Liquid Cooling Container Specfications-A
2024-08-29
1MW/2MWh Liquid Cooling Container Project Specifications
Content
1 Product Introduction.........................................................................................................
2 Explosion Diagram............................................................................................................
3 Electrical system design ....................................................................................................
4 Thermal management methods...........................................................................................
5 Fire Fighting Method..........................................................................................................
6 Battery Container Dimensions ............................................................................................
7 Battery box into the cluster installation and container lifting....................................... ............
1. Product Introduction
1.1 Introduction
This projectis a 1MW/2MWh energy storage system with a non-walk-in design. The system includes PACK warehouse, electrical warehouse, liquid cooling unit warehouse,safety fire warehouse, etc., which facilitates equipmentinstallation and meets the requirements ofsafe,reliable and long-termoperation of the entire system. , can be applied to application scenariossuch as peak shaving and valley filling, peak load regulation and frequency modulation on the power generation side, grid side and userside, demand side response, and renewable energy grid integration for 2 hours and above.
Figure 1 Schematic diagram of container layout
The container layout is as shown in the picture above, using a weather-resistant steel profile tailor-welded box solution. The main material of the box is SPA-H. The dimensions 6058*2438*2896.
The container energy storage power station should include energy storage battery units, BMS battery management systems, fire protection systems, thermal management systems, converging power distribution systems, ventilation systems, video surveillance, etc., using a non-walk-in modular design to integrate the relevant aspects ofthe above systems. The equipment isintegrated into a 20-foot battery prefabricated cabin. The standard unit of the battery prefabricated cabin has its own independent power supply system, temperature control system, heat insulation system, flame retardant system, fire alarm system, electrical interlocking system, mechanical interlocking system, Automatic control and safety assurance systems such as safety escape systems, emergency systems, and fire protection systems.
Figure 2 Distribution of various equipment in the container
The container is equipped with 6 battery clusters, and the battery cluster installation method is shown in Figure 3 below. Each battery cluster consists of 1 high-voltage box, 8 PACK boxes, BMS, inter-box collection, power wiring harness, etc., and is arranged horizontally on the container mounting frame. The high-voltage box is equipped with a battery cluster management unit inside, which is used for precharge contactor control, main circuit contactor control, cluster current collection, cluster temperature and cell voltage status reporting to the overall control, and protection and alarming according to the set protection thresholds. Function, communicates with battery system level master control through CAN bus.
1.2 Design standard
Container design should comply with but not be limited to the following standards:
》 GB 4208-2017 Enclosure protection class (IP code)
》 GB/T 5226.1-2019 Mechanical and Electrical Safety Mechanical and Electrical Equipment Part 1: General Technical Conditions
》 GB/T 2900.33-2004 Electrician's Terminology Power Electronics
》 GB/T 191-2008 Packaging, Storage and Transportation Graphic Marking
》 GB/T 1413-2008 Series 1 Containers Classification, Dimensions and Mass Ratings
》 GB/T 1835-2006 Series 1 Container corner pieces
》 GB/T 4171-2008 Weathering resistant structural steel
》 ISO12944 Corrosion Protection of Steel Structures with Color and Varnish-Protective Coating Systems
》 GB 50116-2013 Design specification for automatic fire alarm systems
》 GB 51048-2014 Design specifications for electrochemical energy storage power stations
》 GB 17467-2010 HV/LV pre-assembled substations
》 GB/T 20138-2006 Protection level of electrical equipment enclosures against external mechanical impacts
》 GB 50217-2007 Power engineering cable design specification
》 GB50168-2006 Cable line construction and acceptance specification
》 GB/T 23932-2009 Metal-faced insulated sandwich panels for construction
》 GB/T 9978-2008 Fire resistance test methods for building components
》 GB/T 7392- 1998 Technical requirements and test methods for containers
》 《Electrical design manual for power engineering - electrical primary part》
》 《Twenty-five key requirements to prevent major accidents in electric power production》
1.3 Technical Parameters
The technical parameters of the container are shown in the table below:
Table of technical parameters of containers
Project |
Technical Parameters |
|
1 |
Model |
LFP-1331.2V-46.592KWh |
2 |
System Configuration |
1P416S*6 Clusters |
3 |
Cell capacity |
280Ah |
4 |
Combination method |
6P416S+6 high voltage boxes+1 Battery Collection Panel |
5 |
Magnification |
0.5P |
6 |
Rated capacity |
1680Ah |
7 |
Nominal voltage |
1331.2V |
8 |
Rated power |
1MW |
9 |
Nominal energy |
2.24MWh |
10 |
Dischargeable energy |
2.24MWh |
11 |
Dimension |
L6058*W2438*H2896 |
12 |
Weight |
30T |
13 |
Integration requirements |
PACK Direct installation to meet overall transportation |
14 |
Fire Fighting System |
PACK Class Gas/Water Fire Fighting |
15 |
Thermal management system |
The ambient temperature is controlled at 25±5℃, the maximum battery operating temperature=3℃, the temperature difference=5℃ |
16 |
Battery temperature control method |
Forced liquid cooling |
17 |
BMS System |
3-tier architecture to meet system control, passive equalization |
18 |
Power Consumption Requirements |
Standby loss requirement = 300W, operating energy consumption = 80kWh/day 1 cycle |
19 |
Operating temperature range |
-30~50℃ |
20 |
Storage temperature range |
-30~55℃ |
21 |
Maximum working altitude |
=4000m |
1.4 Overall technicalrequirementsfor container bodies
Container spraying text, color, decoration, according to customer needs to determine.
The steel structure of the container is made of SPA-H weather-resistant steel plate with flat roof structure, which is convenient for stacking.
Container shell meets three layers of protection: primer is zinc-rich paint, intermediate paint is epoxy paint, outside paint is acrylic paint, and the bottom frame is asphalt paint.
Container wall panels and hatch doors are thermally insulated. Under environmental conditions where the temperature difference between the inside and outside of the cabin is 55°C, the heat transfer coefficient is less than or equal to 1.5W/(m2 ·°C).
The thickness of the insulation material meets the following requirements: Side Wall, Partition Wall: rock wool, thickness 50mm; PACK Door: rock wool, thickness 50m; Bottom Plate, Top: rock wool, thickness 50mm.
The interior paint shall be zinc rich primer (thickness 25µm) + epoxy resin paint (thickness 50µm) with a total film thickness of not less than 75µm.
The total film thickness should not be less than 75µm. Exterior paint to be zinc rich primer (thickness 30µm) + epoxy resin paint (thickness 40µm) + chlorinated plasticized rubber or acrylic top coat (thickness 40µm) with a total film thickness of not less than 110µm.
Table 1 Design parameters for corrosion protection of container bodies
Basic Material |
Type |
Name |
Number of construction lanes |
Dry film thickness (μm) |
Metal structure
|
primers |
HAZ01 Epoxy zinc rich primer (high zinc) |
2 |
80 |
intermediate paint |
HA01 Epoxy ferruginous intermediate paint |
3 |
120 |
|
top coat |
SB02 Aliphatic Polyurethane Anti-corrosion Top Coat |
3 |
100 |
Figure 4 Container anti-corrosion measures
Base plate load
The base plate is subjected to the following static loads without plastic deformation or damage
Battery rackbottomloading:>3500kg/m
Load-bearingcapacityatthebottomoftheconvergencecabinet:>1000kg/m:;
Remainder: >1000kg/m:.
Top plate load
The top plate is subjected to the following static loads without plastic deformation or damage
Concentrated load: 3kN/0. 18m2 (on 600mm*300mm area)
Thermal insulation: Container wall panels, hatch to take thermal insulation measures to deal with the use of temperature regulation system, the temperature inside the container to control the temperature at 5 ℃ ± 5 ℃ ~ 30 ± 5 ℃.
Anti-corrosion: The overall structural framework of the container are made of high-quality steel processing. In the actual operating environment, the actual effective service life of the container is not less than 20 years (only refers to the overall structure of the container).
Fire resistance: the container shell structure, heat insulation and heat preservation materials, internal and external decorative materials are all flame retardant materials.
Earthquake-proof: the container will be lifted, load-bearing and running test before leaving the factory, which can ensure that the mechanical strength of the container andits internal equipments can meet the requirements of the transportation and earthquake conditions.
The mechanical strength of the container and its internal equipment meets the requirements, and there is no deformation, abnormal function, no operation after vibration and other faults.
Battery containers are installed with lighting fixtures and accident lighting fixtures. The lighting fixtures are explosion-proof type, and the lighting wires are concealed through the tubes.
Battery container installation of lighting switches, distribution boxes
Battery containers have ventilation devices. Exhaust device and air inlet can close the air duct to save energy and keep the room temperature when not exhausting air.
The door of the battery container opens to the outside with a solid door made of non-combustible or incombustible material.
Battery containers are equipped with fire extinguishers, fire alarms, temperature detectors and smoke detectors.
Battery container box needs to be grounded, the foundation needs to do a good job of grounding row.
1.4.1 Container specification and dimension
Table 2 Container (high bay) size specifications
Name |
Project |
L( mm) |
W( mm) |
H( mm) |
N.W( kg) |
10 ft. container |
External dimensions |
3004 |
2438 |
2896 |
1750 |
Internal dimensions |
2840 |
2352 |
2690 |
||
20 ft. container |
External dimensions |
6058 |
2438 |
2896 |
3480 |
Internal dimensions |
5898 |
2352 |
2690 |
||
30 ft. container |
External dimensions |
9274 |
2438 |
2896 |
4100 |
Internal dimensions |
9114 |
2352 |
2690 |
||
40 ft. container |
External dimensions |
12192 |
2438 |
2896 |
4700 |
Internal dimensions |
12031 |
2352 |
2690 |
||
45 ft. container |
External dimensions |
13716 |
2438 |
2896 |
5700 |
Internal dimensions |
13556 |
2352 |
2690 |
1.4.2 Container box structure composition
1.4.2.1 Container door structure composition diagram
Figure 5 Schematic diagram of container door structure
1.4.2.2 Container Mechanical Interface Features
The container meets the basic installation requirements for crane installation, and provides two fixing methods: bolts and welding. The bolt fixing points and welding points are reliably connected to the nonfunctional conductors of the entire container (container metal shell, etc.). At the same time, users are provided with at least 2 grounding points in the form of copper bars that meet the most stringent power standards.
Sufficient manholes are reserved inside the container to allow construction and O&M personnel to work underneath the container. The exact location and dimensions of the manhole inside the container are clearly indicated in the drawing documents.
The energy storage containers shall have a protection class of not lessthan IP55, a corrosion protection class of C5 and comply with the relevant provisions of IEC 60529.
1.4.2.3 Grounding design
The container is supplied with a copper grounding strip. Grounding copper can be reliably connected to the entire container of non-functional conductive conductors (normally non-electrically charged container metal shell, etc.), while the container in the form of a copper row to provide the user with four grounding points, to provide users with grounding points must be with the entire container of nonfunctional conductive conductors to form a reliable equipotential connection, grounding points are located in the container's diagonal position. The grounding points are located diagonally across the container.
A partial view of the grounding copper row isshown in the figure below:
Figure 6 Partial view of grounding copper bar
1.4.2.4 Lightningprotection design
The roof of the container is equipped with a high-quality lightning protection system with reliable connection, which is connected to not less than two grounding copper rows provided by the container to the user through the grounding flat steel or grounding round steel, and the effective cross-sectional area of the conductor in the grounding system is not less than 250mm.
Surge protection modules are installed on the line. Surge protector, also known as lightning protector, is a kind of electronic device to provide safety protection for all kinds of electronic equipment,instrumentation, communication lines. When electrical circuits or communication lines because of external interference suddenly produce a spike in current or voltage, the surge protector can conduct in a very short period of time shunt, so as to avoid surge damage to other equipment in the circuit.
Figure 7 Schematic diagram of surge protector
2. Exploded diagram
Figure 8 Exploded view of container layout
3. Electrical system design
3.1 Introduction to high-pressure box
The high-voltage box assembly is mainly used to connect the input of cluster-level power battery and output to the convergence cabinet assembly, and integrates plastic case circuit breaker, DC contactor, fuse, AC/DC switching powersupply, pre-charging resistor, BMS mainframe, high-voltage connectors and box, etc., which form the high-voltage box control assembly.
The total power level of the high voltage box reaches 1500V/250A, and the external shape and installation hole size is W*H*D=481mm*230mm*580mm (including lugs), and the center distance of lugs installation size is W*H=458mm*130mm.
Each cluster is equipped with a high-voltage box containing the cluster management unit and electrical components for the management and protection of the entire cluster.
Figure 9 High voltage box appearance and installation hole dimensions
3.1.1 Front Panel Definition
S/N |
Port Definition |
Functional Description |
Remark |
1 | B+ | Battery cluster input positive terminal | Connect the positive terminal of the battery cluster |
2 | B- | Battery cluster input negative terminal | Connect the negative terminal of the battery cluster |
3 | P+ | PCS Input Positive | Con nect PCS Positive |
4 | P- | PCS Input Negative | Connect PCS Negative |
5 | AC input | BMS Power supply | Connection to utility power 220V |
6 | AC air switch | BMS Power supply switch | Manual control on/off |
7 | Circuit breaker | Battery Cluster Switch | Manual control of on-off, can be equipped with hand-operated, can also be used to |
disconnect the shunt excitation. | |||
8 | Operation | BMS operating indication | Green light |
Indicator Light | |||
9 | Alarm indicator | BMS warning indication | Red light |
10 | To SBMU | CAN communication, power supply and address | BMS Communication |
assignment with SBMU slaves | |||
11 | To SBAU | CAN communication with SBAU stack control | BMS Communication |
12 | Debugging interface | For program upgrades and host computer testing |
3.1.2 Electrical schematics
The main functions of each electrical component in the high voltage box are as follows:
(1) Fuse: When (overload or short-circuit) current exceeds a specified value, the heatgenerated by itself causes the fuse to fuse, and can be quickly acted within a specified periodof time to disconnect the circuit of an electrical appliance
(2) load switch: a simple arc extinguishing function, with the disconnection of load current(can be used to open and close the load current less than a certain number of times theoverload current, usually 3-4 times), can not be quickly disconnected or disconnected from theshort-circuit current; can form a clear point of disconnection, often used in conjunction withfuses for short-circuit protection
(3) circuit breaker: a mechanical device switch (can break the overload current, short-circuitcurrent leakage protection and other functions); mainly rely on the addition of currenttransformers with the secondary equipment to protect the
(4) contactor: a small current to control the operation of high-current “automatic switch”, andin the circuit with other components to form the role of security protection mechanism
(5) Pre-charge resistor: Limit the main circuit current during the high-voltage process.
(6) Pre-charging relay: Controls the opening and closing of the pre-charging circuit.
Figure 10 Electrical schematic diagram of high voltage box
3.1.2 Topology diagram
The topology of the high voltage box is divided into high voltage and low voltage parts, and the functions of each part are described as follows:
Charging and discharging circuit: with main positive fuse, DC molded case circuit breaker, to realize the discharge circuit protection and maintenance isolation, with main positive and main negative relay, to realize the main circuit discharge control.
Equalizing resistor circuit: the main positive relay is connected in parallel with an equalizing resistor circuit at both ends of the main positive relay, and there is a pre-charging relay and pre- charging resistor, which can realize the equalizing resistor when there is an imbalance between the battery clusters to achieve the voltage equalization.
AC power supply circuit: AC220V power supply output, switching power supply for the back-end controller, circuit breaker electric operation and breaking to provide energy Source.
AC/DC power supply circuit: Converts AC power to 24V and supplies power to all back-end controllers and the sorting driven by the controllers.
Alarm Operation Indicator: Accurately anticipates the electrical operation of the high voltage box. Communicate with the slave control in the battery box in the cluster: accurately grasp the information of the batteries in the battery box.
Communicate with the master control: report information about the batteries in the cluster.
Figure 11 Main circuit topology of high voltage box
Figure 12 Low-voltage circuit topology of high-voltage box
3.2 Introduction of Battery Collection Panel (BCL)
This BCL is used to manage the high voltage inputs and outputs between the battery system and the PCS, the power up and down flow of the DC side of the energy storage system, and the protection logic for the high voltage.
Figure 13 Dimensional drawing of combiner cabinet
3.2.1 Function description
Supports 220VDC power input to power the internal UPS power supply in the busbar.
The UPS supplies power to the switching power supply (220Vac), which is converted by the switching power supply to indirectly supply power to the main control module (24Vdc recommended).
Supports the power supply to the high voltage box, the supply voltage is 220Vac, indirectly to the main control module.
Supports communication with PCS inverters, EMS systems and dynamic loop testing equipment.
Support circuit breaker opening/closing and status monitoring, and display the status by indicator lamps.
Summarize the real-time data information of the whole system, support the processing of battery stack status data, and realize the management and control of battery charging and discharging after completing the processing.
Support emergency stop control function, in case of emergency, press the emergency stop switch button on the outside of the cabinet to stop the operation of the whole energy storage system.
Support convergence cabinet LED status indication, including power, status, fault three status indicators.
The SCU master control module installed in the convergence cabinet has isolated LAN, CAN, RS485, RS232, TF card and USB interfaces, which realizes communication, data storage and protection with the RCU master control module, MM10 display and control module, PCS inverters, EMS system and dynamic loop testing equipment, and can realize internal data, operation data storage and power-down preservation, and support program upgrade and data export. Support program upgrade and data export.
The MM10 display module installed in the convergence cabinet is equipped with isolated LAN, micro USB, USB, TF card interfaces, and a 10.1” display to realize communication with the SCU master control module and data display of the entire battery system.
Over-voltage, under-voltage, differential voltage, over-current, under-current, over- temperature, low temperature, temperature difference, short circuit, insulation, relay diagnostics and other alarms and protections for batteries (single, module, cluster, stack).
3.2.2 Topology diagram
Figure 14 High-voltage topology diagram in the Battery Collection Pan
Figure 15 High-voltage topology diagram in the junction cabinet
The functions and functions of the main electrical components in the junction cabinet are as follows:
(1) DC disconnect switches: used in the main circuit to provide system-level direct current disconnection.
(2) Main positive fuse: with the main disconnecting switch to play the role of short-circuit protection of the circuit.
(3) DC lightning protector: protects DC lines and switches against lightning strikes.
(4) DC lightning protection fuse: protects the system in case of lightning protection failure or short circuit.
(5) the AC branch circuit openers: play a normal role in breaking, and in the line short-circuit and other situations to play a protective role
(6) Switching power supply: Used to supply power to BMS and other controllers.
(7) AC lightning protector: protects DC lines and switches from lightning strikes.
(8) AC lightning protector protection switch: lightning protector failure or short circuit to protect the system.
(9) Fan: Used to dissipate heat in the convergence cabinet
4. Thermal management methods
4.1 Function description Liquid cooling composition
The ambient and internal temperature of the battery system will directly affect its normal operation, including battery cycle life, power output, capacity, safety and reliability. Therefore, in order to obtain the best performance and life of the battery, thermal management is needed to control the temperature of the battery system within a specific range to reduce the uneven temperature distribution within the battery, in order to improve battery aging and eliminate potential risks.
4.2 Liquid cooling composition
The liquid-cooled thermal management system consists of liquid-cooled panels, liquid-cooled units, liquid-cooled piping, high- and low-voltage wiring harnesses, and coolant, and the following measures are taken to address the problem of liquid-cooled leakage:
(1) Liquid-cooled fittings using automotive-grade anti-leakage cooling pipeline quick-connect fittings can ensure that when the energy storage system is in operation, the risk of liquid leakage is minimized.
(2) Liquid level sensors are installed in the expansion tank of the liquid cooling unit, and the liquid cooling unit will alarm if there is any liquid leakage.
(3) The battery pack is designed with IP67 protection level to ensure that there is no impact on the system in case of liquid leakage. Battery pack liquid-cooling plate is aluminum profile (aluminum extrusion), integrated base and liquid-cooling plate function, which, liquid-cooling plate and sheet metal cover in the middle of the installation of gaskets, through the screws to lock the sealing formation of IP67; at the same time, liquid-cooling plate will also be done to ensure that the liquid -cooling plate sealing performance good airtightness testing. The liquid cooling plate of the battery pack adopts “serpentine” flow channel, and the coolant adopts 50% water + 50% glycol. The liquid cooling system makes the coolant flow through the liquid cooling plate to cool or heat the battery pack through certain thermal management strategy.
Figure 16 Schematic diagram of pipeline & unit
4.3 Liquid cooling strategy
When Tmax ≥ 35°C, the liquid cooling unit enters the refrigeration mode, the compressor is turned on, and the high-temperature and high-pressure refrigerant is discharged from the compressor, enters the condenser for condensation, releases heat and cools down, is throttled and decompressed through the expansion valve, and then enters the evaporator The refrigerant absorbs heat in the evaporator and evaporates, then flows back to the suction port of the compressor to complete a refrigeration cycle. At this time, the water pump in the water circuit is turned on and the PTC heater is not turned on. The coolant is cooled in the plate evaporator and then enters the liquid cold plate of the battery pack to cool the battery and take the heat out, thereby achieving the purpose of cooling the battery. When Tmax≤25℃, the cooling mode will be stopped.
When Tmin≤0℃ (Tmin≤5℃ in charging mode), the liquid cooling unit enters the heating mode, the compressor is turned off, the water pump and PTC heater are turned on, and the coolant is heated by the PTC heater and then enters the battery cold plate. Heat the battery. This mode is suitable for situations where the battery needs to be heated when the battery temperature is too low. When Tmin≥10℃ (Tmin≥15℃ in charging mode), the heating mode will stop.
Figure 17 Liquid cooling and liquid heating flow chart
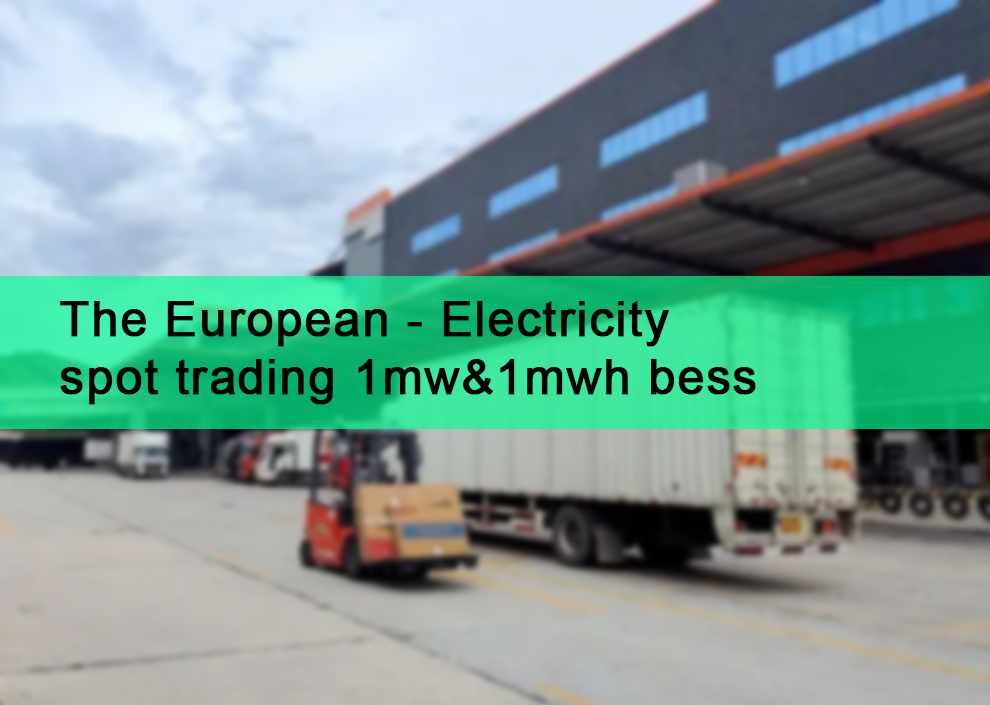
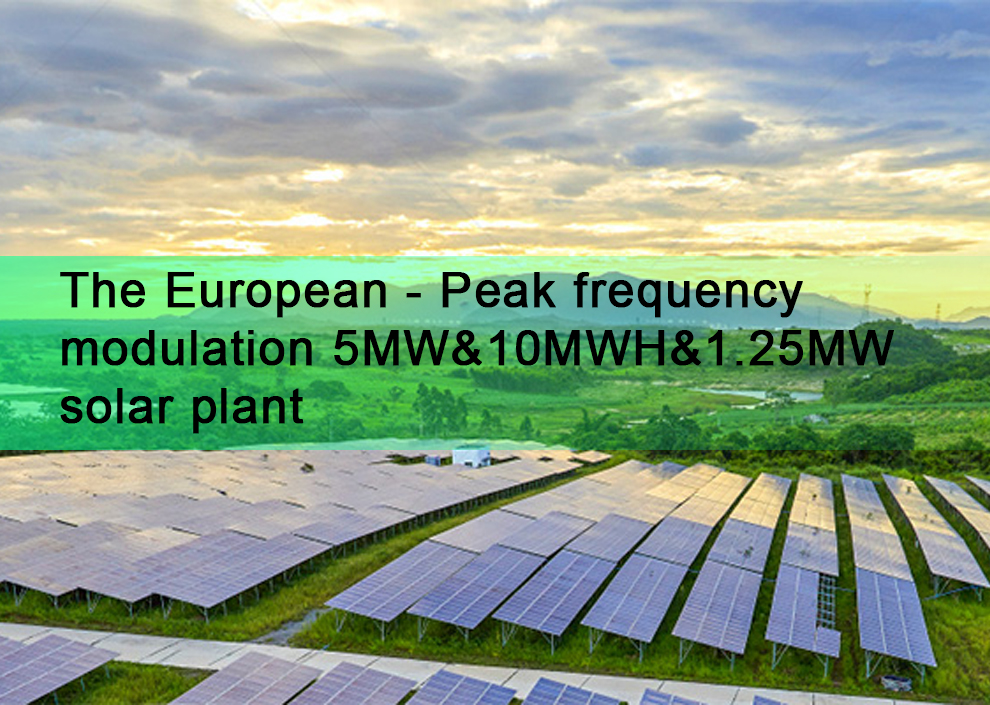
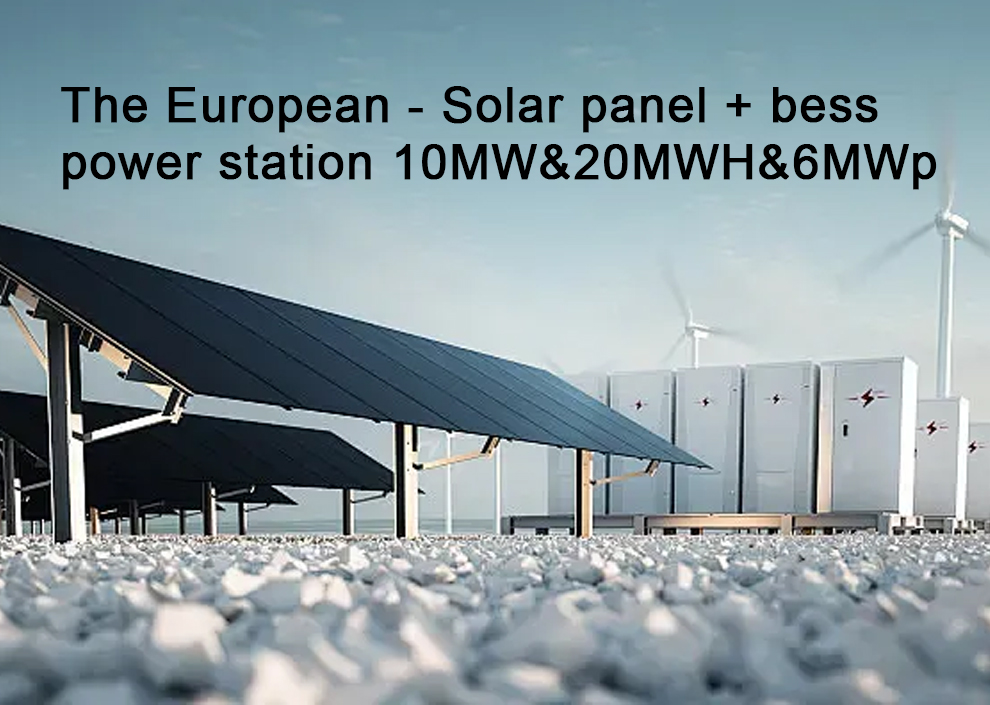
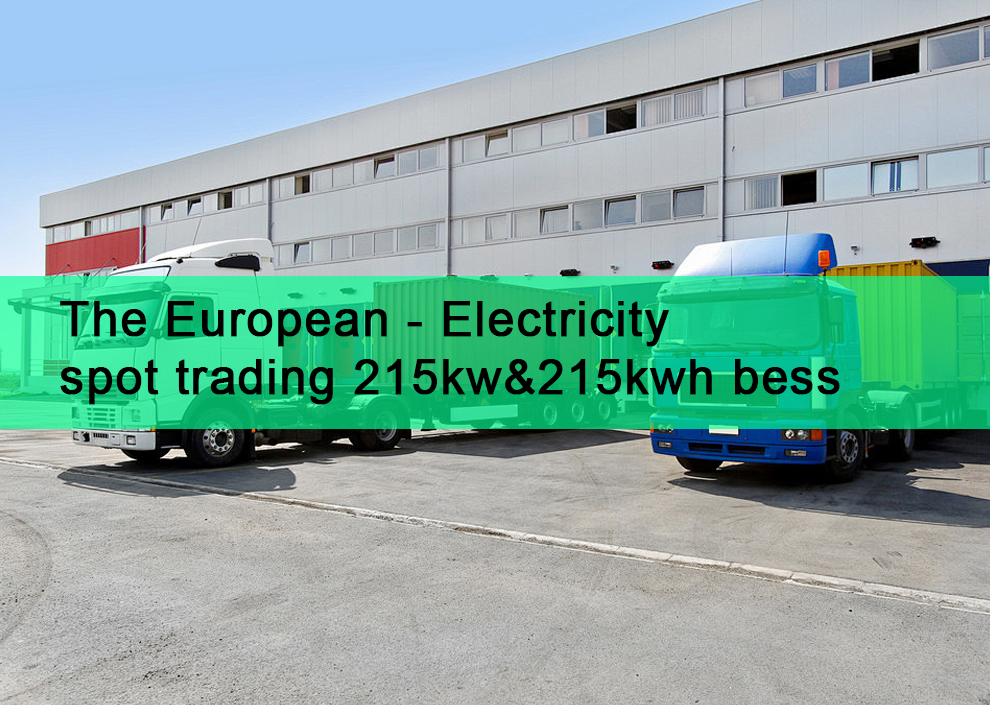
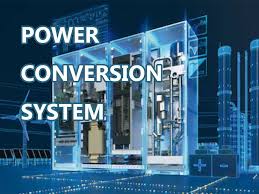