1MW 2MWh Liquid Cooling Container Specfications-B
2024-08-29
1MW/2MWh Liquid Cooling Container Project Specifications
Content
1 Product Introduction.........................................................................................................
2 Explosion Diagram............................................................................................................
3 Electrical system design ....................................................................................................
4 Thermal management methods...........................................................................................
5 Fire Fighting Method..........................................................................................................
6 Battery Container Dimensions ............................................................................................
7 Battery box into the cluster installation and container lifting....................................... ............
5 Fire fighting methods
5.1 Functional Description
The fire extinguishing system abandons Heptafluoropropane or Perfluorohexanone as the fire extinguishing inhibitor, and adopts YEC-1 liquid fire extinguishing medium as the fire extinguishing inhibitor to be sprayed directly into the interior of the battery box where the thermal runaway occurs, so as to realize rapid fire extinguishing, and effectively solve the problems of cooling down and secondary re-ignition.
Figure18 PACK Level Fire Topology
The whole fire-fighting system consists of three parts: PACK level fire-fighting system, cabin level fire-fighting system and linkage system. The core of the system is: fire alarm control device (referred to as fire alarm control device), hydrogen, carbon monoxide and smoke and temperature sensing composite fire detection device (referred to as composite detector), electrochemical fire suppression device (referred to as suppression device), the functions of which are described as follows:
Fire alarm control device: the information processing center of the whole fire protection system. The main function is to receive and process detectors and other alarm signals internally, issue linkage commands, and monitor the working status of the whole system; externally, it communicates with the BMS system, the fire platform of the station and other upper systems, and the last system-related information.
Composite detector: divided into PACK-level detectors and cabin-level detectors. The PACKlevel detector uses a two-in-one carbon monoxide and smoke detector, and the cabin level uses a five-in-one detector with two explosion-proof methods of intrinsic safety and explosion- proof, which can detect carbon monoxide, hydrogen, smoke, temperature, and VOC gases at the same time. Suppression device: mainly composed of fire extinguishing medium and pump unit.
5.2 Firefighting strategy
PACK level fire protection:
Each PACK is placed in the form of a two-in-one detector, and the detector detection parameters are carbon monoxide and temperature. The detector connects the electrical connections (power +, power -, CAN_H, CAN_L, puncture valve control) through the adapter. The alarm strategy of the PACK detector is based on the principle of "early detection, timely disposal", and the specific trigger conditions and The execution actions are shown in the table below:
Prealarm level | Trigger conditions | Execute action |
Level 1 Pre-alarm |
Carbon monoxide concentration > 190ppm |
The alarm unit of the controller warns the police, and the display unit emphasizes the display of the relevant. The display unit highlights the relevant parameters, and at the same time transmits the warning signal to the monitoring platform in the fire control room |
Level 2 Pre-alarm |
Carbon monoxide concentration> 500ppm or temperature>65℃ |
The alarm unit ofthe controller alarms, and the display and control unit highlightsthe relevant excessive parameters; it linksthe shunt trip,turns on the audible and visual alarm, and transmitsthe early warning signalto the controlroom monitoring platform at the same time; |
Level 3 Pre-alarm |
Carbon monoxide concentration > 800ppm and {temperature > 75℃ or temperature rise greater than 3℃/s (lasting at least 10 seconds)} |
The alarm unit of the controller alarms, and the display control unit highlights the relevant excessive parameters; it links the shunt trip, turns on the audible and visual alarm, and sends the early warning signal at the same time. The signal is transmitted to the fire control room monitoring platform; the PACK fire extinguishing action is executed; |
Cabin firefighting:
The cabin is detected by three explosion-proof 5-in-1 composite detectors arranged on the roof, and the fire extinguishing method is perfluorohexanone + water diffusion irrigation with external fire fighting water source. As the fire fighting of the cabin is related to the safety of the whole cabin, it is also the last line of safety defense. Therefore, the alarm strategy of the cabin program is based on “cabin alarm, automatic fire extinguishing + manual handling”, the specific trigger conditions and execution actions.
Pre-alarm level |
Trigger conditions |
Execute action |
Level 1 Pre-alarm |
One detector in the system uploads a level 1 warning signal. The detector generates a level 1 warning condition: Hydrogen concentration > 150 ppm orCarbon monoxide concentration > 150 ppm |
Sensors increase the sampling frequency to provide real-time insight into changes indetector concentrations |
Level 2 Pre-alarm |
At least two detectors with different numbers in the system upload a secondary warning signal. Detectors generate a Level 2 warning condition: Hydrogen concentration > 200 ppm or Carbon Monoxide concentration > 190 ppm |
The alarm unit of the controller warns the police, and the display and control unit emphasizes the display of the relevant exceeding parameters; the controller turns on the sound and light alarms inside and outside the station as well as the smoke exhaust fan and electric louvers, and at the same time transmits the warning signals to the monitoring platform of the fire control room; |
Level 3 Pre-alarm |
At least two different numbered detectors in the system upload a three-level thermal runaway alarm signal. The detector generates a three-level alarm condition: Smoke alarm with (hydrogen concentration>500 ppm or carbon monoxide concentration>490 ppm or VOC >1000 ppm or temperature>70°C) |
The alarm unit of the controller will alarm, and the display unit will display three levels of alarm information; Link the BMS to disconnect the power supply of the cluster level, PCS and excitation release, shut down the air conditioner, smoke exhaust fan and motorized louver, and activate the sound and light alarm; Execute cabin-level perfluorohexanone spraying action; Manually confirm the fire situation, turn on water diffusion irrigation, and at the same time transmit the alarm signal to the monitoring platform of the fire control room; |
6. Battery container dimensions
Figure 19 Battery Container Dimensions
7 Battery Row Installation and Container Lifting
7.1 Battery box into cluster installation
Battery pack push out into the container workflow: will be equipped with a battery pack into the cluster tooling to move to the front of the container, maintain an appropriate distance. Through the remote control switch to adjust the position of the battery pack into the front end of the installation of the front pallet rack, start the switch to launch the beam, the battery pack will be launched into the container, to be stabilized after the battery pack to control the remote control switch to exit the beam, and then through the bolts will be mounted on the battery pack hole and the battery clusters fastened to the battery pack.
Figure 20 Battery box into the cluster installation diagram
When the battery pack (box) is put into the container, the box will be lifted to the rollerbed and fixed first; then the roller bed will be fork lifted to the container installationposition by motorized forklift, and positioned by the positioning pin on the top of theroller bed, and the stepping motor A will drive the roller bed through the chain sprocketuntil it is in place.
After positioning, the stepping motor A drives the roller bed through the chain sprocketand conveys the roller bed to the container body until it is in place.
When the battery pack is pulled out, the lifting ring is assembled to the battery pack(box), and then the roller bed is forked up to the container mounting position by themotorized forklift, and positioned by the positioning pins at the top of the roller bed,and the hook on the winch is hooked onto the lifting ring, and the stepping motor Bdrives the winch to drive the hook to pull out the battery pack (box), and in the processof pulling, the stepping motor A synchronizes to drive the rolling bed to pull out thebattery pack (box), until the fixed position of the roller bed.
Stepper motors A/B can be driven individually or simultaneously with the push of abutton.
7.2 Container lifting
Figure 21 Spreader installation process
Figure 21 Schematic diagram of container lifting
The wire rope selected for this lifting program is D=32mm high carbon steel wire rope, steel core strength ≥1570Mpa, to meet the 《(GB/T8918-2006) 》important use of steel wire rope” related requirements.
The structure lifting through the two beams and 4 wire rope combination, the center of gravity of the container is about in the middle, in line with the safety of the force and normal operation, can ensure that the container lifting process is smooth and can work normally.
Table 2 List of spreaders
S/N |
Name |
Quantity |
Material |
Remark |
1 |
Crossbeam |
2 |
20# |
I-beam with sealing plate load 90T |
2 |
Shackle |
8 |
Alloy Steel |
60T |
3 |
Wire Rope |
4 |
High Carbon Steel |
Diameter 32 wire rope, single load 50T |
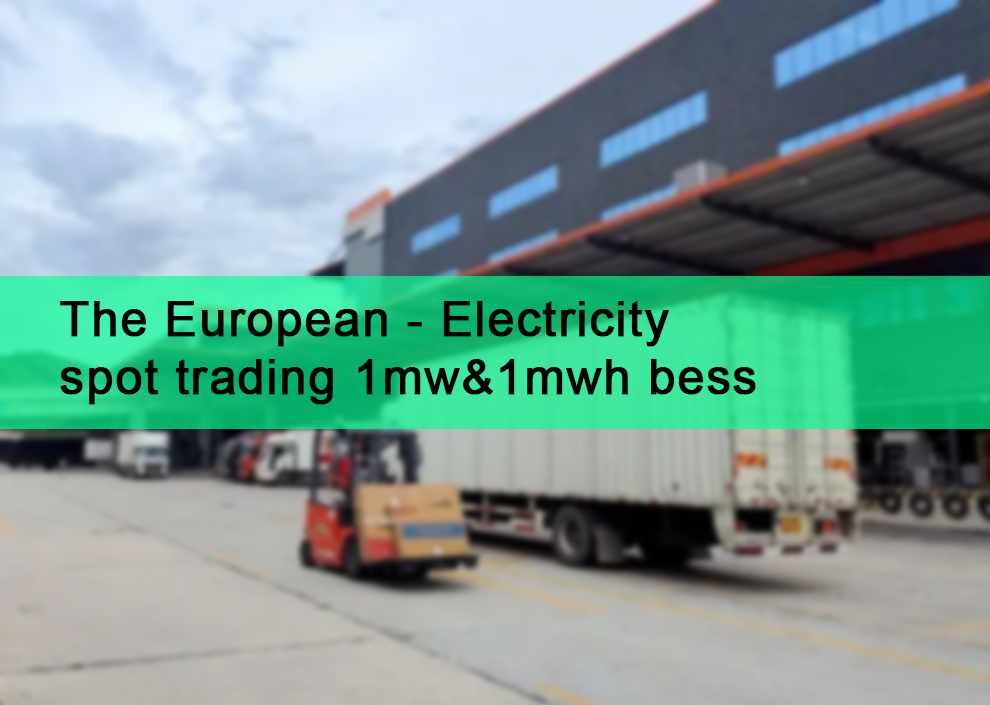
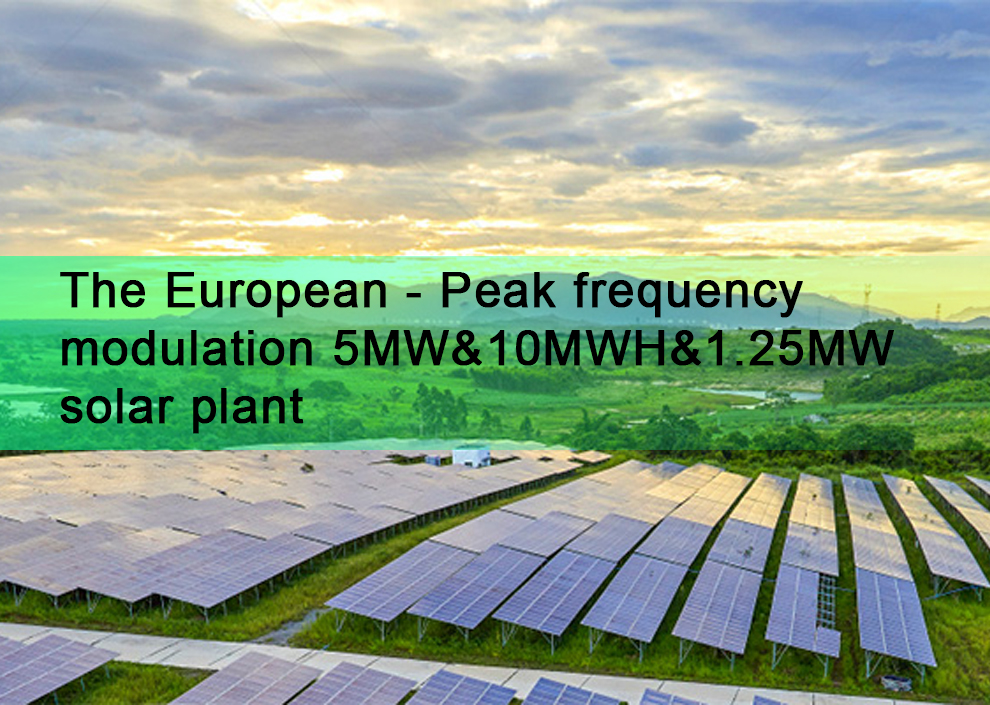
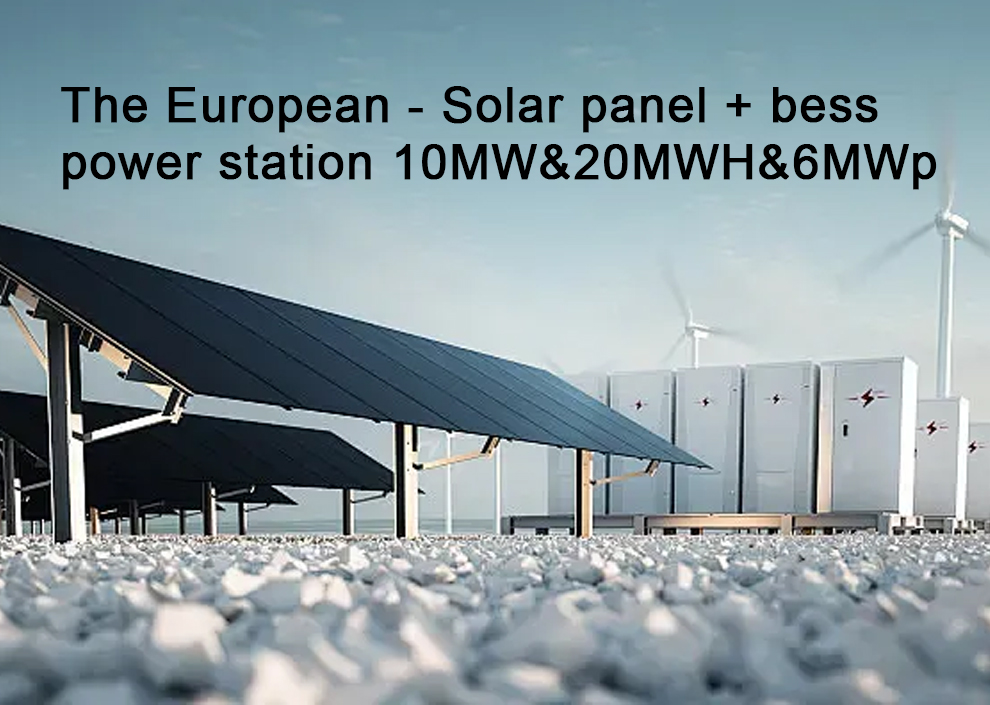
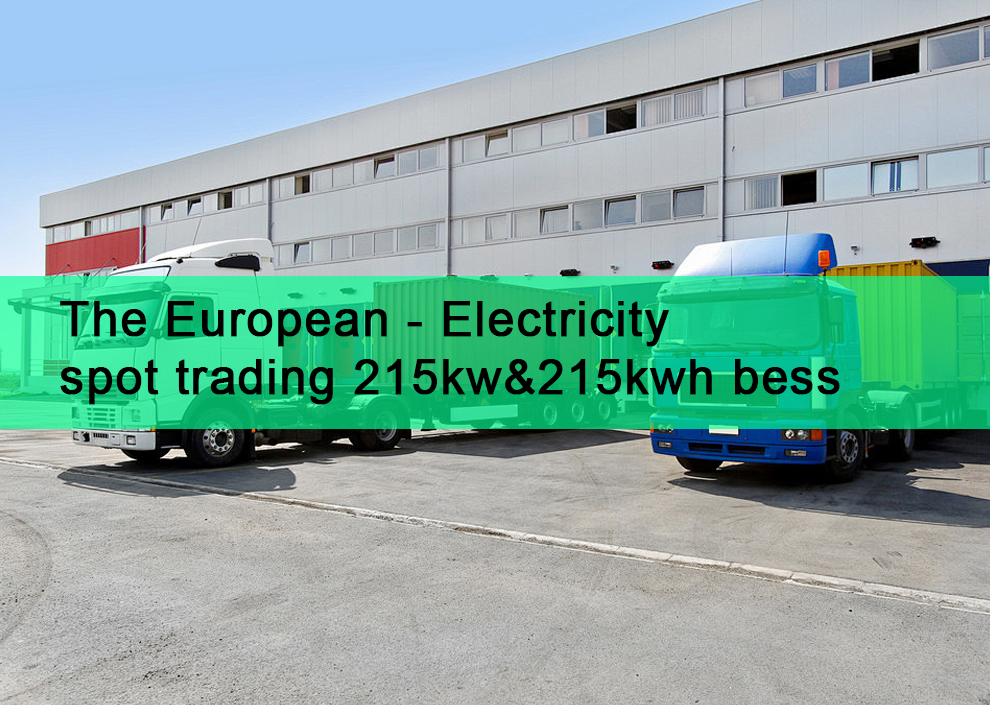
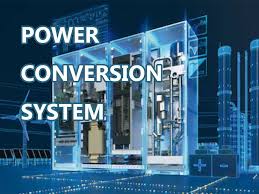